An inking system is a component of a printing press that is responsible for applying ink to the printing plate or cylinder. It ensures the controlled and uniform distribution of ink onto the image areas of the plate, which is then transferred to the substrate during the printing process. The inking system plays a crucial role in achieving accurate and consistent ink coverage for high-quality prints.
The specific design and configuration of the inking system vary depending on the printing process and press type. Here are some key elements commonly found in an inking system:
- Ink Fountain or Ink Supply: The ink fountain or ink supply is a reservoir that holds the ink. It provides a constant supply of ink to the other components of the inking system. The ink fountain may have mechanisms to control ink flow, such as ink keys or ink ductors, which regulate the amount of ink being supplied.
- Ink Rollers: Ink rollers are rotating cylinders or rollers that pick up ink from the ink fountain and transfer it to other parts of the inking system. They can be made of metal or rubber and are designed to evenly distribute ink onto the plate surface. Ink rollers can include different types, such as the form roller, distributor roller, and inking roller, each serving a specific function in the ink transfer process.
- Oscillating or Vibrating Mechanism: In some printing presses, the ink rollers are equipped with an oscillating or vibrating mechanism. This helps ensure a uniform distribution of ink by preventing ink buildup or streaking on the rollers and facilitating better ink transfer to the plate.
- Doctor Blade: In certain printing processes, such as gravure or flexography, a doctor blade is used to remove excess ink from the surface of the plate or cylinder. It helps maintain a consistent ink layer and prevents unwanted ink from transferring to non-image areas.
- Ink Ducts and Ink Keys: Ink ducts and ink keys are mechanisms used to control the flow and distribution of ink across the ink rollers. They allow for precise adjustment of ink volume and ink flow to achieve the desired ink coverage on the plate.
- Ink Agitation or Circulation: Some inking systems incorporate mechanisms for agitating or circulating the ink in the ink fountain. This helps prevent ink settling and ensures consistent ink properties throughout the printing process.
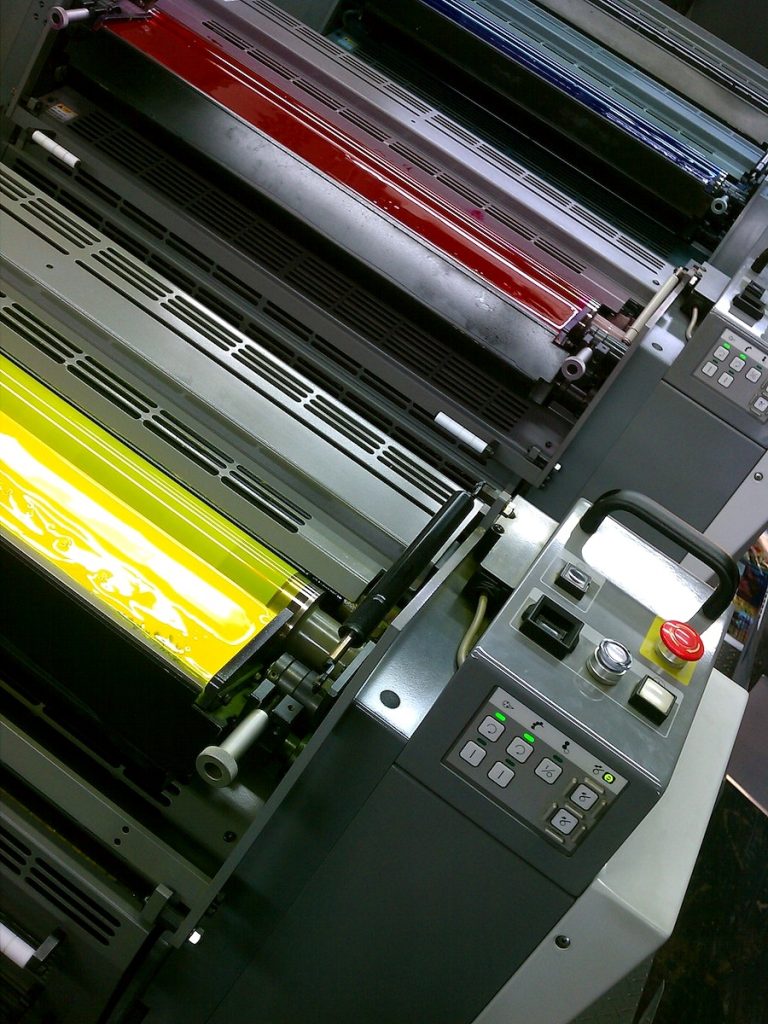
The inking system works in conjunction with other components of the printing press, such as the plate cylinder, blanket cylinder, and impression cylinder, to transfer the inked image from the plate to the substrate. Proper ink distribution and control in the inking system are essential for achieving accurate color reproduction, sharpness, and consistency in the final printed output.